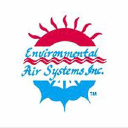
Manufacturing Safety Manager
Automate your job search with Sonara.
Submit 10x as many applications with less effort than one manual application.1
Reclaim your time by letting our AI handle the grunt work of job searching.
We continuously scan millions of openings to find your top matches.
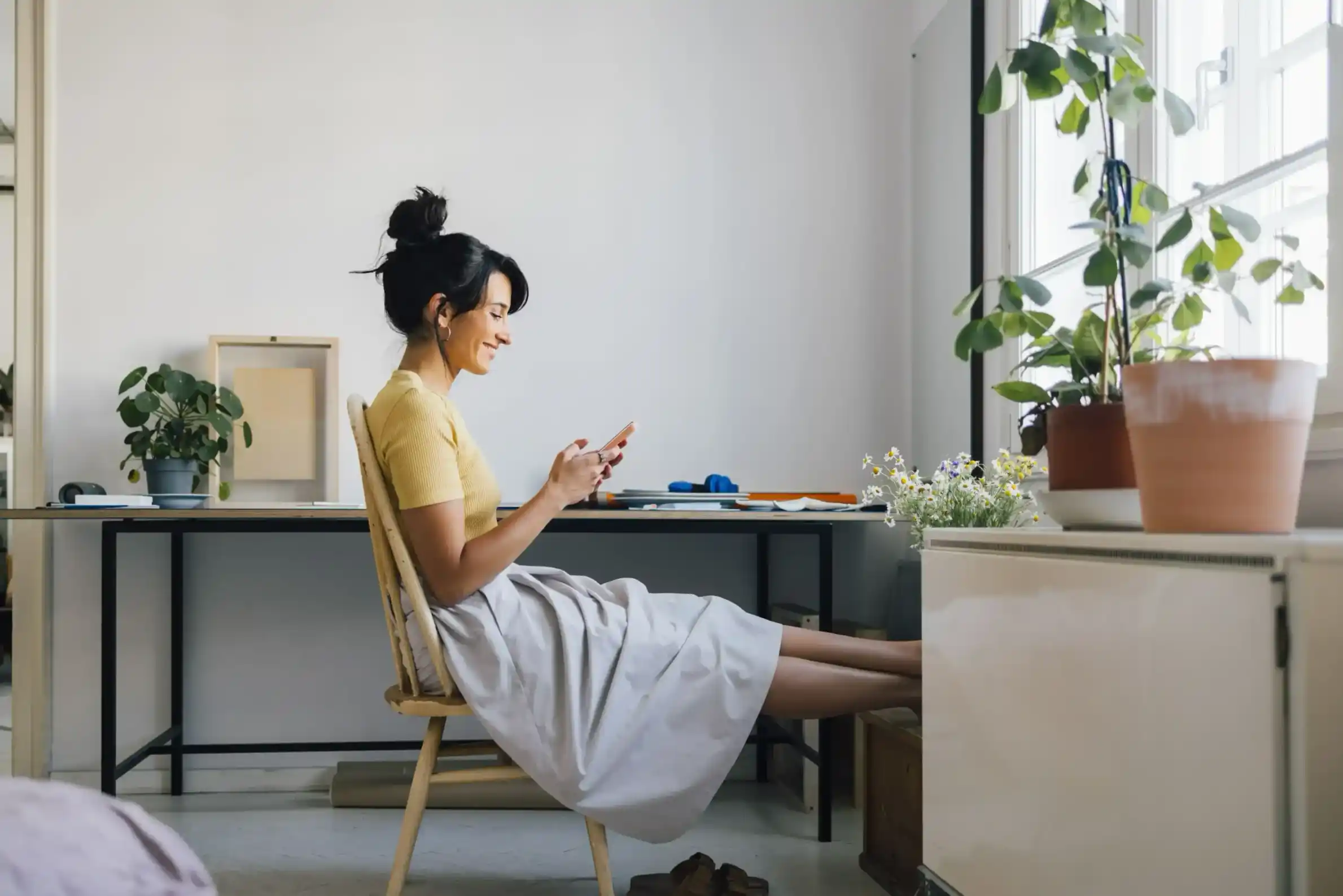
Job Description
Education & Certifications
Bachelor’s degree in Occupational Health and Safety, Environmental Science, Industrial Engineering, or a related field.
Preferred certifications:
Certified Safety Professional (CSP)
Associate Safety Professional (ASP)
Certified Industrial Hygienist (CIH)
OSHA Certification
Experience
Several years of experience in manufacturing safety management or a related field.
Prior roles such as Safety Coordinator, EHS Technician, or Environmental Specialist can be beneficial.
Key Responsibilities
Develop and implement safety policies to ensure compliance with OSHA and other regulations.
Conduct safety training for employees on workplace hazards and emergency procedures.
Perform risk assessments and identify potential hazards.
Investigate workplace incidents and recommend corrective actions.
Ensure equipment & machinery meet safety standards.
Maintain safety records and report safety metrics to management.
Ensure the Safety Coordinator thoroughly oversees Plant Inspections, Safety Documentation, and follow-ups for concerns throughout plant operations on the day-to-day implementation and management of safety programs and policies.
Monthly Safety Meeting – Safety Team, Mentors, Cadets, Weekly Production Meeting
Track Department Safety Metrics / Trends.
Tracking safety team work hours/time management.
Ensure Third Party plant inspections are being conducted annually & resolved.
Routinely inspect plant operations
Investigate First Aids with Safety Coordinators/ Supervisors, determine root cause & corrective measures.
Elevate the development training plan for coordinators and technicians.
Maintain OH&S and regulatory compliance through operations.
Conduct Quarterly Mock OSHA
SDS Review – New Products
Maintain ISO 45001 Internal / External Records
Review and address concerns & Recommendations from monthly safety meetings.
Advanced Responsibilities
Safety Program Development: Design and implement comprehensive safety programs tailored to manufacturing environments.
Emergency Preparedness: Develop evacuation plans, fire safety protocols, and hazardous material handling procedures.
Incident Investigation: Conduct root cause analysis for workplace accidents and implement corrective actions.
Essential Skills
Technical knowledge of safety regulations, hazard identification, and emergency response planning.
Soft skills such as leadership, communication, and problem-solving.
Ability to conduct audits & inspections to ensure compliance.
Proficiency in data analysis & report writing
Regulatory Knowledge
OSHA Compliance: Must be well-versed in Occupational Safety and Health Administration (OSHA) regulations.
Environmental Health & Safety (EHS): Understanding of EPA, NFPA, and ANSI standards.
Industry-Specific Regulations: Knowledge of ISO 45001 (Occupational Health & Safety Management Systems).
Technical Expertise
Risk Management: Ability to assess ergonomic risks, machine safety, and chemical hazards.
Safety Audits & Inspections: Conduct regular workplace audits to ensure compliance.
Data Analysis: Use safety metrics to track trends and improve workplace safety.
Leadership & Communication
Employee Engagement: Foster a culture of safety through training and awareness programs.
Cross-Department Collaboration: Work with HR, Operations, and Engineering teams to integrate safety into daily operations.
Crisis Management: Lead incident response teams and coordinate with emergency services.